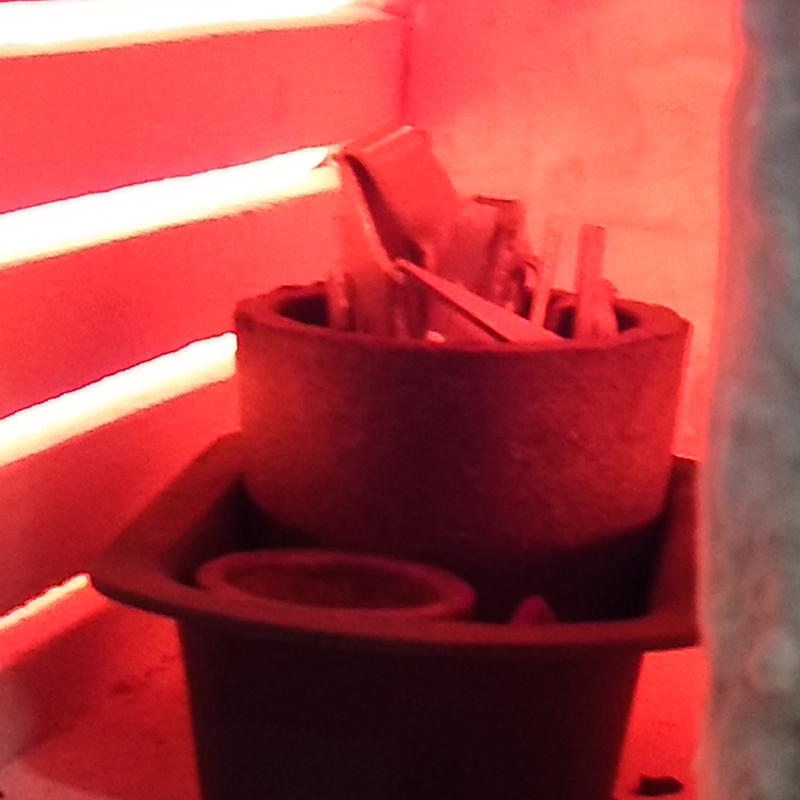
The story begins here.
But to summarize : I got my hands on a furnace, and melted some glass and aluminum. It was supposed to sit in my studio, but for reasons long-forgotten, we stopped over and now it’s in my living room, to the overlapping amusement and chagrin of family, friends and assorted neighbours.
Moving on, I got my hands on a set of graphite crucibles, that Josh very kindly picked up for me, as well as better safety equipment.
The weekend rolled around and Josh turned up, and I am so thankful he did. He spent the next hour tearing up all the scrap aluminium sheet leftover from previous projects, (lasercut metal heatsinks, custom sheet metal components, some slot-and-assemble pieces, etc.) I had a few square feet of intricately cut and immensely tiresome scrap that that he snipped, bent, broke or tore apart, into bite-sized pieces.
I had created some molds in plaster and white cement to try out casting objects as well.
We fired up the furnace, got the aluminum melted, properly contained in a graphite crucible and not a shatterprone terracotta pot. And then we poured.
I was reminded that metals have fantastically high surface tension, and the molten metal clung to itself far more than to any details in the mould, etc. The next set of molds will be deeper to take up a large enough shot that the Al enters the cavity in full. It may not be enough to capture details, but large scale features will work.
In any case, we got a few good chunks, and we cycled them a couple of times. With aluminum, multiple firings are possible because, unlike glass, we didn’t have to let it cool slowly over a longer period to anneal.
The ghost of the Harappan seal, minus any detailed features.
A hook, and a bubble that got trapped under a layer of thin metal.
Aluminum is easier to work with than glass, as far as the furnace is concerned. The new equipment helps a lot, but there’s still a long way to go before I am casting my own knickknacks.