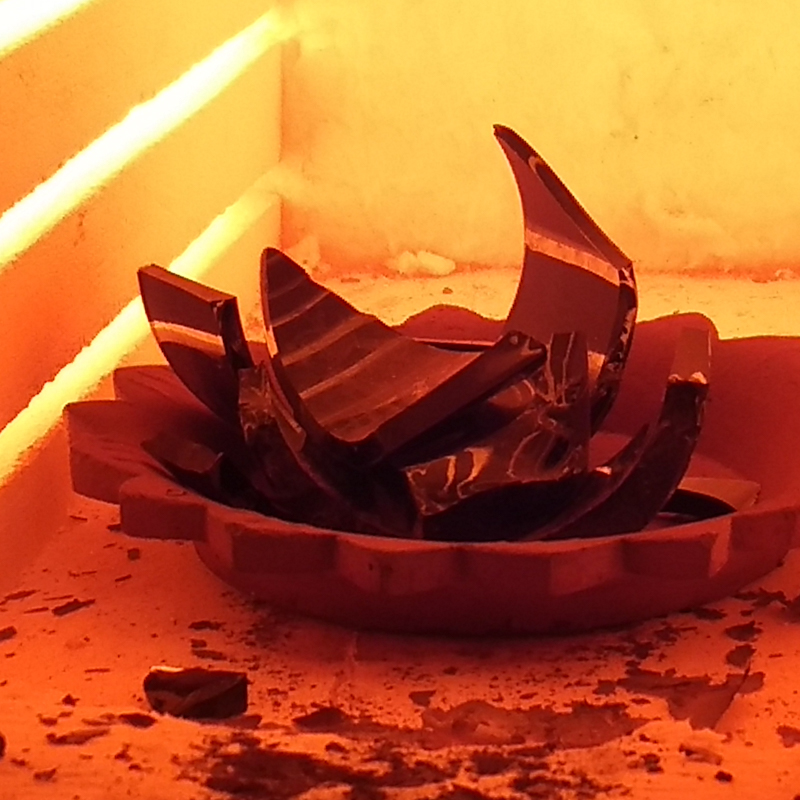
A while ago, V (from V for Wood) and I picked up a muffle furnace from a neighbour of his who was moving countries. An actual, melt-your-brains (and a lot more) furnace. It’s a small enough chamber, but goes to about 1100 C, and is good for a lot.
We brought it home first, intending to shift it to the studio soon, but the damned thing is heavy, and now a long-time resident of my living room.
Over the next few weeks, I made a higher-grade extension box to power it from the nearest 16 A source, did some reading, convinced the original manufacturer to talk to me and give some advice, and, long story short, finally we got it running.
Since I had no particular molds and whatnots to work with, the first few trials were just slumping glass in terracotta and earthenware from the local kumbharwada. Surprisingly, it worked, but the clay items would crack after a few cycles.
During one such session, Josh had come around to help out, and I had gotten my hands on an earthen plate with embossed patterns. I also had a broken mug of black glass lying around. And chunks of aluminum sheet leftover from lasercutting custom heatsinks.
I wanted to try out if the glass could be slumped and cast and if it would take the pattern. So the broken glass was loaded up.
But I also wanted to see what would happen if we mixed Aluminum and glass. Aluminum melts at 700 C and glass starts to soften at 650 C. We were limited to one good firing a day, and then cooling off over 24 hours to anneal the glass properly (“properly” is debatable, this was a completely amateur attempt, but we were doing what we could.) So impatience got the better of us and we decided to add the Al as well to this.
Well, it worked, kinda ! We took the temperature to 800+ C, so the glass would soften well and the Al would be completely liquid. Turns out, molten aluminum floats on glass, because when we finally took it out, the layers were distinct though we had mixed them up intermittently. (Not that we expected any fine intermixing, but I was hoping for some swirls. But the Al was liquid long enough to just flow around.) However, they do seem to have bonded, and the glass definitely picked up the pattern in the plate.
This is the upper side of the whole piece, and the aluminum texture looks wild. The glass layer is visible as the black patch, so the glass was still viscous enough to maintain it’s uneven thickness as it was slumping.
These early practice runs were a great learning experience. Josh has been a great help, in physical strength as well as tips and ideas. My stock of broken glassware is undiminished, and I hope I start putting it to good use soon.